Before CNC machining was invented, all metalworking fabrication processes were completed with NC (Numerical Controlled) machines. The concept of was introduced in 1967 but the first CNC machines were introduced in 1976. Since then the popularity of CNC grew very significant and it was recognized as the industry standard in 1989. Today, we will tell you the brief history of CNC machining.

In 1948, representatives of the US Air Force (USAF) visited the Parsons Corp. headquarters and Parsons was awarded a contract to make new and innovative wing designs for military applications. This, in turn, led to a series of USAF research projects at the Massachusetts Institute of Technology (MIT) Servomechanisms Laboratory, culminating in the construction of the very first numerically-controlled, albeit awkward, machine prototype. To accomplish this, Parsons purchased a Cincinnati DK Series, 28-inch Hydro-tel verticle-spindle contour milling machine consisting of a table and spindle that moved along X, Y and Z-axes. Over the next two years, the Cincinnati was disassembled, significantly modified, retrofitted, and reassembled. As application studies proceeded, the prototype was augmented to produce a motion of the head, table, or cross-slide to within 0.0005″ for each electrical impulse fed by the director. To ensure the prototype was functioning as instructed, a feedback system was added. In response to movement, synchronous motors geared to each motion produced voltage. This voltage was sent back to the detector for comparison to the original command voltage.
By 1953, enough data had been culled to suggest practical, aeronautic applications, and the Cincinnati prototype, which employed a Friden Flexowriter with its 8-column paper tape, tape reader, and vacuum-tube control system, became the de facto prototype for all successive developments. To this day all CNC controlled machines, even the most sophisticated still require three basic systems to operate: a command function system, a drive/motion system, and a feedback system.
Although CNC gained slow acceptance throughout the ’50s, in 1958 MIT Servomechanisms Laboratory developed g-code, which has become the most universally used operating language for CNC devices.
In the early ’60’s the Electronic Industry Alliance (EIA) standardized g-code and computer-aided design (CAD) became a nascent technology providing a firmer technology foundation. As a result, CNC soared and began steadily supplanting older technologies.
By the ’70s, minicomputers such as the DEC PDP-8 and the Data General Nova made CNC machines more powerful and cost-effective. US companies responsible for the CNC revolution, focused on high-end equipment. German and Japanese companies sensing the need, began producing smaller, less expensive CNCs, and since 1979 they have been outselling the United States.
Finally, PCs have now made CNC controls even cheaper, making way for the use CNC-controlled machines for the hobby and general purpose markets. CNC control language now known as LinuxCNC (formerly known as Enhanced Machine Controller, or EMC2) continues to thrive, as are many other CNC technologies.
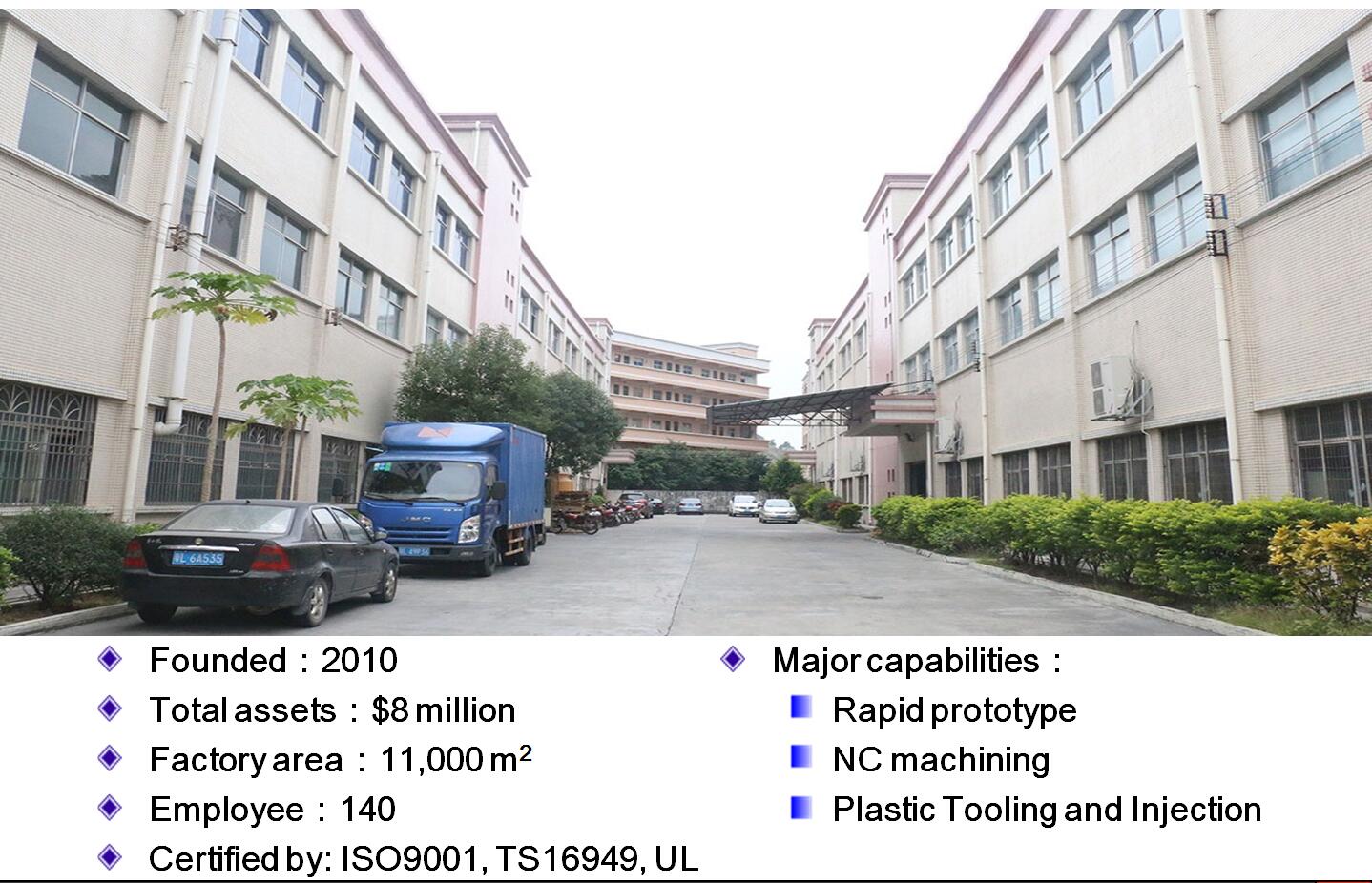
JasonMould is one of the best plastic injection molding makers that offer great services to their clients when it comes to manufacturing advanced molding tools. They export their tools to different parts of the world and have become one of the most famous names in the industrial sector.
Inquiry Contact:
Contact person: James Yuan
Company name: JasonMould Industrial Company Limited
Address: LongGang Village,LongXi Town,BoLuo County,HuiZhou City,GuangDong Province, China
Telephone: 86-752-6682869
Email: info@jasonmolding.com
Website: https://www.jasonmolding.com
Article Original From:https://www.jasonmolding.com/brief-history-of-cnc-machining/